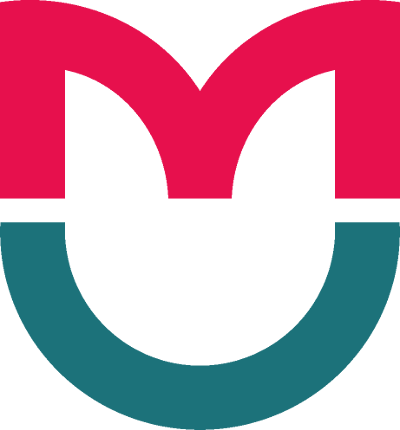
This article is an open access article distributed under the terms and conditions of the Creative Commons Attribution license (CC BY).
OPINION
Prospects for the use of long-living printed temporary orthopedic structures
Pirogov Russian National Research Medical University, Moscow, Russia
Correspondence should be addressed: Amir M. Enikeev
Ostrovityanova, 1, str. 9, Moscow, 117997, Russia; moc.liamg@tra.tamots.rima
Author contribution: Proskokova SV — project management, manuscript editing; Enikeev AM — literature search and analysis, manuscript writing; Pirogov AE, Kuliev RM — manuscript editing.
Treatment of partially edentulous patients is a pressing issue of prosthetic dentistry [1, 2]. The use of non-removable temporary structures in prosthetics proved to be not only important, but also uncontested stage of the effective high-quality treatment. During the period between the start of tooth preparation and permanent fixation of non-removable structures it is necessary to manufacture and use the temporary prostheses showing high mechanical stability and protecting the prepared teeth against bacterial infection and irritants of various types: thermal and chemical. The temporary prostheses ensure safety of the pulp, protection of the marginal periodontium, predictable shaping of the marginal gingiva, lack of negative effects on the components of the temporomandibular joint (TMJ) and the mastication muscles. Furthermore, temporary structures make it possible to preserve or reconstruct the lost occlusion and aesthetics. Currently, the arsenal of prosthetic dentists includes a large number of materials used for temporary structures.
The study was aimed to present the main temporary prosthetics methods and the advantages of 3D-printed structures.
The search for scientific papers on the issue was conducted in the catalogues of scientific electronic libraries (https://www.elibrary.ru, https://pubmed.ncbi.nlm.nih.gov) for the years 2017–2024.
The search in Elibrary involving the use of the “3D-печать” word phrase and the dentistry filter yielded 205 results (among them 195 for the years 2017–2024), the search performed using the “временные коронки” word phrase yielded 310 results (among them 150 for the years 2017–2024), the search in Pubmed involving the use of the “3d printed crowns” word phrase yielded 389 results (among them 362 for the years 2017–2024), and the search performed using the “Temporary crowns” word phrase yielded 1716 results (among them 344 for the years 2017–2024) (fig. 1).
A total of 153 papers were selected by manual sorting.
When performing advanced search in the set prepared, we managed to obtain the following information about the paper types: dissertations — 2 (1.3%); books — 15 (9.8%); conference papers — 29 (18.9%); patents — 11 (7.1%) (fig. 2).
Conventional approach
Conventional approach involves the use of the acrylic-based plastics and composites with various types of polymerization.
The methyl methacrylate-based acrylic plastics are most often used in the laboratory manufacture of temporary structures. The crowns and dental bridges made of plastics of this type are characterized by high strength and color stability and can be also used over a long recovery period.
Ethyl methacrylate is used in temporary prosthetics for short-term application in the oral cavity. Lower heat emission and the decreased shrinkage rate represent the advantages of this material.
The Bis-acrylate-based materials for temporary prosthetics are very popular. This two-component material is based on the methyl methacrylate-derived multifunctional acrylic esters. The Bis-acrylate-based materials are produced primarily in the form of cartridges for the 4 : 1 or 1 : 1 dispensing and mixing systems, which enables quick and easy manufacture of temporary systems when there is silicone index. Lower strength characteristics and the need to manufacture a silicone index represent disadvantages of such materials.
Composite materials with low-temperature polymerization are also produced in the form of cartridges for the 4 : 1 dispensing and mixing systems or in the form of syringes as fluid variants of dental filling composites. These materials are characterized by positive effects peculiar to modern dental meterials: are easy to administer to the cavity due to their texture [3].
Digital approach
As for digital approach, the structures manufactured by CAD/CAM milling represent one option for temporary prosthetics.
CAD is the Computer Aided Design, i.e. creation of a virtual structure. CAM is the Computer Aided Manufacturing. CAD/ CAM represents the advanced technology for production of scaffolds or complete dentures by computer aided design and milling on the numerically controlled machines (CNC).
The polymethyl methacrylate (PMMA) plastic is the main material for the temporary structure milling. PMMA is used for both short-term restorative care and the long-living structures. This material is flexible and very strong. Difficulty to achieve enough strength of adhesion with the prepared tooth stump is a disadvantage.
The emergence of the 3D printing technology represents the next stage of development of the digital temporary prosthetic approach. Today, the technology makes it possible to manufacture full removable prostheses, crowns, suprastructures for implants, and navigation templates. The prototyping results obtained are superior to the equivalent use of conventional materials [4].
The photopolymer resin 3D printing belongs to the broad category of light polymerization in baths. The concept is based on the photosensitive resin capability of solidifying under exposure to light energy.
Currently, there are several 3D printing options: SLA, DLP, LCD. The SLA (laser stereolithography, stereolithography apparatus) technology is based on directing the UV laser beam onto the bath with polymer resin, which leads to polymerization at a certain point. Then the working surface is shifted downward by 0.025–0.300 mm, and the laser ensures polymerization of the next layer. The process continues until the model construction is over [5].
DLP is the Digital Light Processing. Radiation emitted by the digital projector selectively affects the liquid photopolymer resin contained in the special container through the print area. The resin is solidified layer-by-layer at the exposure sites, and the 3D model is steadily constructed. The distinctions of the technology are the relatively small working area, high printing speed, wide range of compatible expendables.
LCD technology is the youngest among photopolymer printers. Initially, LCD emerged as a more affordable analogue of the DLP technology, since the operation principles are similar. In LCD, the UV LEDs are used that light through the LCD screen to solidify the photopolymer resin. Despite the fact that the LCD screen also constructs the entire layers over the same time, as the DLP 3D printers, the quality of layers depends on the screen resolution. The higher is LCD screen resolution, the higher is printing quality.
Polymer materials are widely used for medical applications. Along with the common technical requirements (melting point, strength, wear resistance, etc.) for medical polymer materials, especially dental materials, there are additional sanitary and hygienic requirements: minimal interaction with bioactive environments, no toxic effects, low solubility, minimal sorption properties.
The following components are usually contained in photopolymer resins for temporary prostheses:
Monomeric base. Methacrylate-based monomers are commonly used, such as Bis-GMA (bisphenol A-glycidyl methacrylate) or UDMA (urethane dimethacrylate). These monomers ensure high strength and stability of the resin.
Photoinitiators are substances triggering the polymerization reaction due to light. Camphorquinone (CQ), benzophenone (BP) and 4-methylaminobenzoic acid phenylpropionate (MABBP) are the most common photoinitiators. These absorb light of a particular wavelength and generate free radicals that initiate the polymerization process.
Fillers are represented by particles added to the resin in order to improve its properties. These can be mineral (for example, silicon dioxide), organic (for example, barium sulfate) or synthetic (for example, microglass).
Curative is a substance that accelerates the polymerization process. Benzoyl peroxide or other organic peroxides are commonly used.
Pigments are substances that give the resin a certain color. These can be organic or inorganic.
Additives are supplementary substances that can be added to the resin in order to improve its properties. For example, antioxidants are added to prevent oxidation, plasticizers to improve flexibility, and moisturizing agents are added to prevent dehydration.
Dentistry is widely accepted as the field that can greatly benefit from the 3D printing technologies. In domestic literature, there are many review papers focused on the use of 3D printing. However, there are few papers considering parameters, characteristics, and properties of such materials in detail [6, 7].
The review of foreign literature has yielded much more data. Some studies claim that 3D-printed interim polymer materials show lower flexural strength (FS) compared to the milled interim restoration [8, 9]. However, the 3D-printed interim polymer materials show higher flexural strength compared to the temporary structures made of conventional materials [10, 11]. Multiple studies focused on comparing wear resistance of materials showed lower loss of volume associated with wear and smoother surfaces in the 3D-printed samples [12]. When printing, printers are able to apply layers sized up to a tenth of a micromillimeter to yield a product with a smoother surface, and the time of polishing is reduced compared to milling [13].
Moreover, the 3D-printed materials usually have higher elastic modulus (EM) compared to conventional materials, but the EM does not exceed that of milled materials. As for surface roughness, the 3D-printed materials have a smoother surface compared to the milled and conventional interim materials.
Thus, the data of assessing physical and mechanical properties suggest that 3D resins show better results, than conventional materials. Milled structures are the favorites, except for the prosthesis smoothness.
However, we must not forget about the economic aspect. A number of papers consider the feasibility of photopolymer resin printing [14, 15]. The 3D printing method is cost-effective, and the possibility of manufacturing the necessary structure only without using the plaster model reduces the production time. The amount of photopolymer necessary to manufacture the structure is spent during printing, while about 30% of the block volume constitutes the cost when using milling. Digital approach and the 3D printer availability allow the attending physician to perform all the procedures necessary for treatment in the same clinic without involving third-party dental laboratories and dental technicians.
In our country, the domestically produced photopolymer resins that are cheaper compared to foreign analogues are mainly used. It should be noted that resins produced in Russia are not inferior in their properties to imported materials and are exported to other countries for dental applications. By contrast, manufacturers from China dominate almost completely in the market of the CAD/CAM preforms for temporary prosthetics, due to which the final product becomes more expensive.
The process of improving the printed polymer flexural strength still continues. There are polymer resin modifications, in which the zirconium oxide (ZrO2) nanoparticles are added to various concentrations. Mechanical properties superior to that of conventional printing resin have been revealed, which increase possible lifespan of such structures. These modifications are already available on the market, including modifications produced by the domestic 3D printing resin manufacturers.
CONCLUSION
The use of dental 3D resins is a promising avenue for temporary prosthetics, including that for continuous exploitation. These materials are not inferior to competitors in mechanical properties. The structures are cheaper compared to the CAD/ CAM-milled analogues. This opens the door for the use of effective and affordable prosthetic options.